Nuclear Energy : Dealing with the Elephant(s) in the Room. Dr. Gareth Peel, Director of Waste Management for Veolia Nuclear Solutions tackles this topic in this month's edition of Nuclear Engineering International magazine.
Though the challenges associated with the processing of nuclear wastes remain, investment in technologies can help minimise the legacy impact of nuclear operations through the processing and disposal of civil nuclear wastes.
INTEREST IN NUCLEAR ENERGY HAS increased dramatically over the past few years. As global uncertainty in the oil and gas markets grows, and climate change continues to evolve, investors, governments, energy experts and even environmental activists are taking a fresh look at nuclear energy as a real solution to our energy security crises. What they are finding is that the nuclear industry of today has changed dramatically with major advances in technology mitigating many of the traditional concerns. However, there remains an elephant in the room. What do we do with the waste? It is this question above any other which is challenging investment in the sector today.
Maximising the Waste Hierarchy
Radioactive waste is simply waste which has a radioactive component. While high activity wastes at Sellafield and Fukushima grab the headlines, most radioactive waste falls into the very low and low-level waste categories. Contributing more than 94% of the 5.1M tonnes of waste identified in the current UK radioactive waste inventory it includes many different materials ranging from used gloves and wipes to contaminated land and building materials. This waste, if not treated, creates secondary waste streams due to the infrastructure needed to maintain, repackage and store the materials. A problem exacerbated by adding to the original waste, for example by grouting. Radioactive wastes have limited disposal options. Those which are available in the UK, namely licensed landfill, the low-level waste repository (LLWR) or the geological disposal facility (once built), have limited capacity and are expensive to use. Minimising nuclear waste and diverting wastes to other routes is necessary to reduce costs and maximise the life of nuclear disposal facilities.
Diverting Wastes via Sort and Segregation
Utilising robotics and artificial intelligence to sort nuclear wastes has the potential to deliver safer, faster and cheaper solutions. To drive efficiency nuclear engineers are increasingly looking to automation technologies. One concept is that of co-bots - robots that work alongside humans and handle simpler repetitive tasks, alerting humans when they need to intervene. Distributing tasks between humans and machines to improve processes has significant benefits in the context of sorting and segregating nuclear waste but delivering it requires technology that allows humans to intervene whilst remaining remote from these hazards.
Veolia Nuclear Solutions (VNS) is making strides in sort and segregation through the automation of its remote manipulator system, DEXTERTM, providing all the benefits of robotic remote capabilities without exposing the operator to the hazardous environment. Developments in this area allow automation to perform the bulk of tasks but also allow for remote, efficient operator intervention. By combining the best of human skill and modern automation technology VNS aims to unlock faster, cheaper, and safer nuclear waste management.
Minimising Waste Volumes
Vitrification is a well-known technology for the processing of nuclear wastes. The technology thermally processes waste materials, reducing the volume by up to 80%, and produces a robust and long-lasting waste form. The radionuclides are captured within a glass matrix ideal for long-term disposal due to the leach resistance and durability of the product. The technology is expensive, but the acceptance criteria is exceptionally wide. This makes the technology attractive for the processing and disposal of problematic waste forms – demonstrating that there are processing techniques available for the most challenging nuclear wastes. Infrastructure costs on storage can be avoided by taking the opportunity to reduce waste volume through vitrification. The challenge is ensuring that the end product is compatible with committed infrastructure including storage, containers, and transport solutions.
GeoMelt® is a vitrification technology processing problematic wastes including asbestos, contaminated soils and reactive metals. Developed by VNS, successful trials have demonstrated the potential for this technology to volume reduce and process a wide range of nuclear wastes, while minimising the creation of secondary waste. In 2022 VNS opened a commercial GeoMelt® vitrification plant in Andrews, Texas. The Andrews facility can accept, process and dispose of nuclear wastes. Due to the proven leach resistance of the product, it is disposed of directly into the Waste Control Specialists landfill on the same site. By reducing process complexity and pre-treatment, while also eliminating problematic by-products, GeoMelt® has made vitrification a cost effective and safe method for treating reactive metal wastes.
Learning from our Past
And when things do go wrong, for example, the Fukushima incident (2011) - we see a sector which is deploying innovation to meet the challenges for clean-up and waste management. In the immediate aftermath of the incident significant challenges had to be overcome to recover contaminated cooling water and to remove active isotopes, specifically caesium and strontium. Whilst effluent processing is well understood, using various filter and ion-exchange media to capture the active media, the challenge at Fukushima was the scale of the problem and the time constraints which drove urgent deployment before active liquids leaked. The challenges at the Fukushima Daiichi plant are immense. The radioactive environment within the reactor means that any technology deployed needs to be robust yet flexible enough to fit through limited openings into the reactor. Mapping the environment, characterising the materials in the reactor and recovering the hazardous waste is a significant undertaking.
In just eight weeks, VNS designed, fabricated and delivered a 1,200 m3 /day external water-cooling system to safely decontaminate the water. Within the six months that followed more than 70% of the caesium from the water had been removed. The plant was declared to be in a safe, secure, cold shutdown status. In 2013, Veolia designed, fabricated, and delivered a 300 m3 /day at-tank Mobile Processing System to decontaminate radioactive strontium. Veolia started operating at Fukushima in early October 2014 and removed more than 99.95% of the strontium from the water.
The constant acceleration of technology development changes the landscape of what is possible to achieve with effluent management and remote handling technologies, from development of servo actuators technologies to the increasing use of digital solutions and to extend the life of existing reactors. Lessons learned from these decontamination applications have direct relevance on civil nuclear operations today, especially reactor decommissioning and contingency planning; technology which has the potential to support plant life extension in a cost-effective and innovative way.
In 2017, VNS was tasked to design, manufacture, test, and deliver two long reach robotic manipulator systems. Used to inspect and repair leaks in the lower levels of the Unit 2 reactor at Fukushima the equipment is designed to operate in an environment which includes water, high radiation, contamination, and damaged infrastructure. In July 2021 VNS, along with partners at Mitsubishi Heavy Industries, delivered to Japan the first remotely operated articulated boom system. This world-leading technology is undergoing testing before being deployed at the Fukushima facility in 2023. The long-armed boom will reach over 21 metres at full extension to help inspect and retrieve fuel debris in the primary containment vessel of reactor 2.
Conclusion
The technologies described in this article, as well as best practice adopted by the sector, is minimising the amount of materials which need to be treated as nuclear waste, and is enabling effective deployment of the waste hierarchy. Further, the sector is learning from its past. Technologies continue to be developed which have the potential to de-risk operations and decommissioning by removing the operator from the hazard and by reducing or fully removing the hazard to minimise the environmental impact of nuclear operations. The progress made gives me confidence that solutions to the nuclear waste challenges we’ve been debating for years are well within reach.
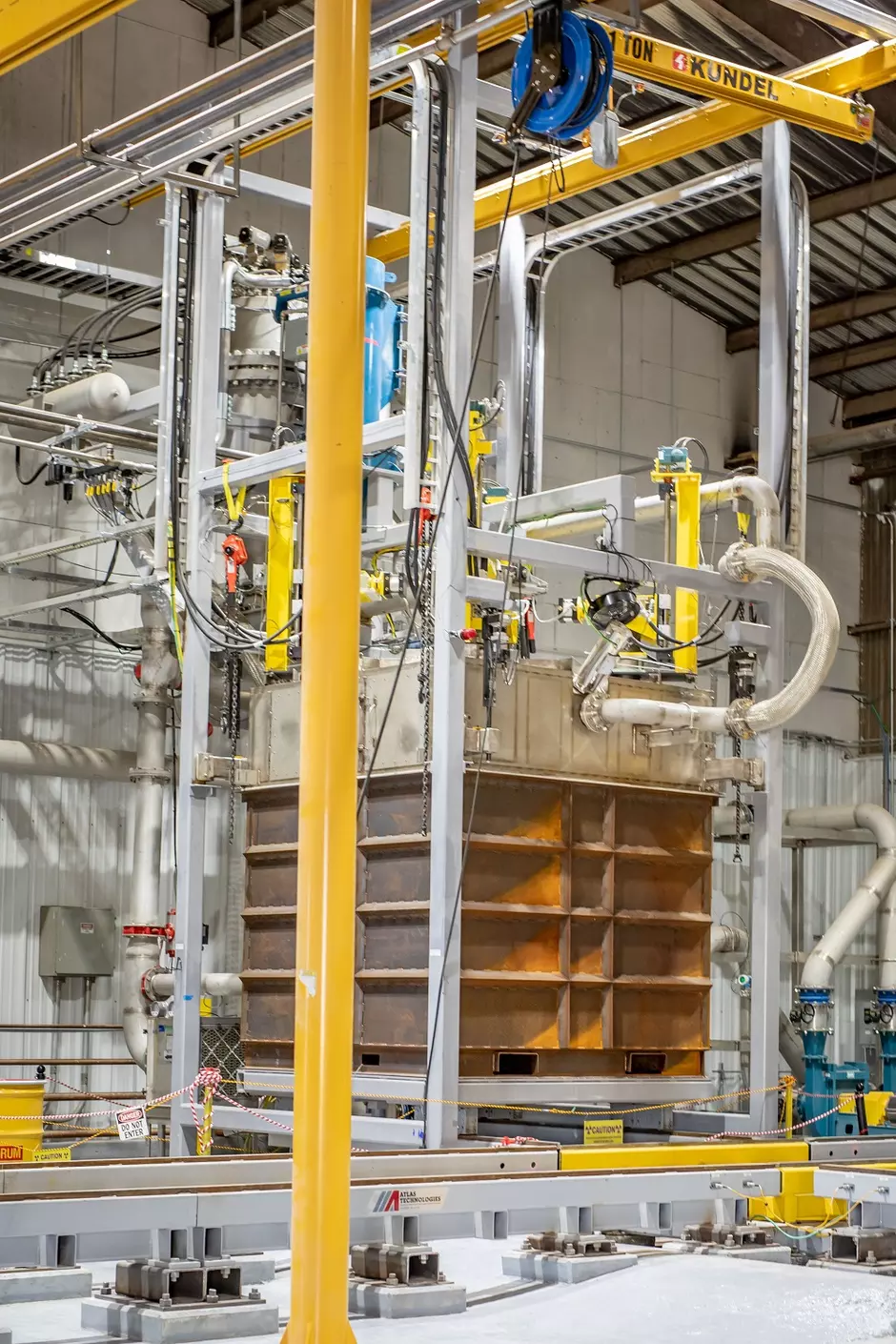
Above : GeoMelt® Melter at Andrews, Texas
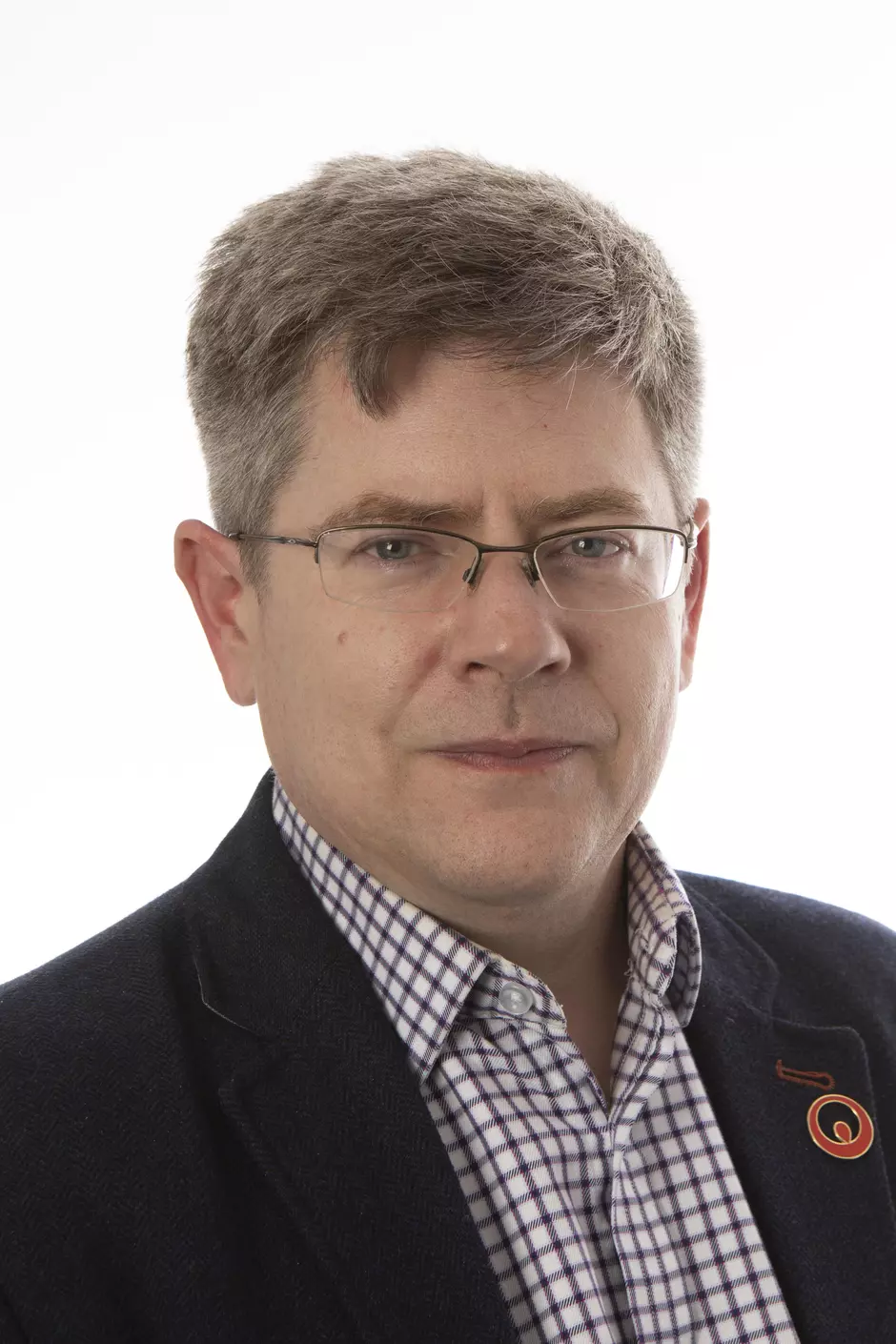
Dr. Gareth Peel - Director of Waste Management
Veolia Nuclear Solutions
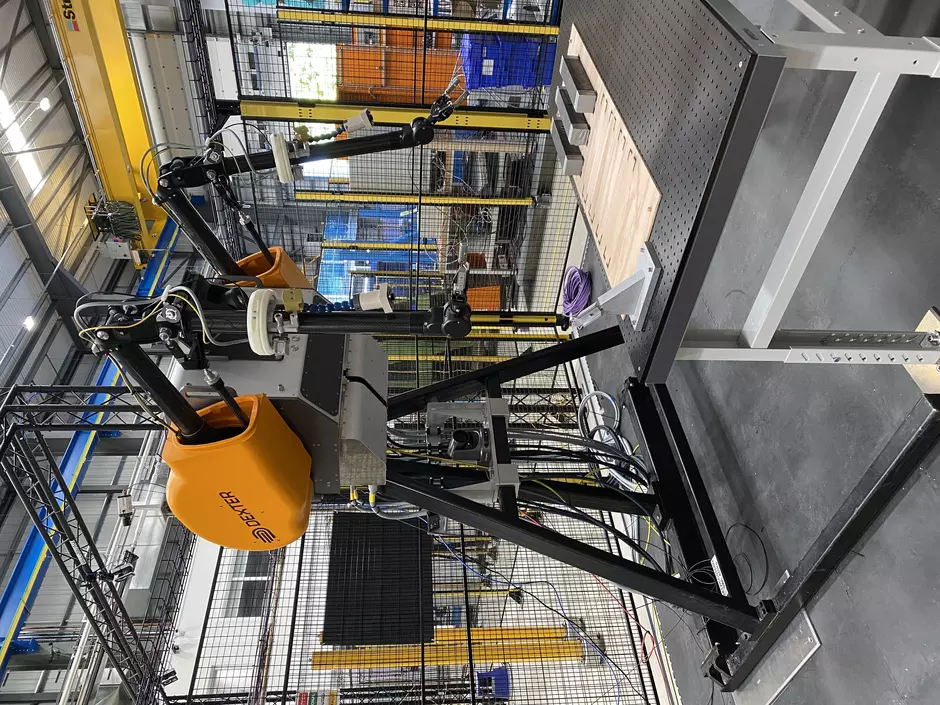
Above: DexterTM